Thermography | Infrared Thermographic Test
Thermography Test for Electrical Panels and Equipment To ensure Electrical Safety, Prevention of Fire and Operational Continuity.
Onsite Thermography Services across India
IFC (World Bank Group) Approved Independent Consultant
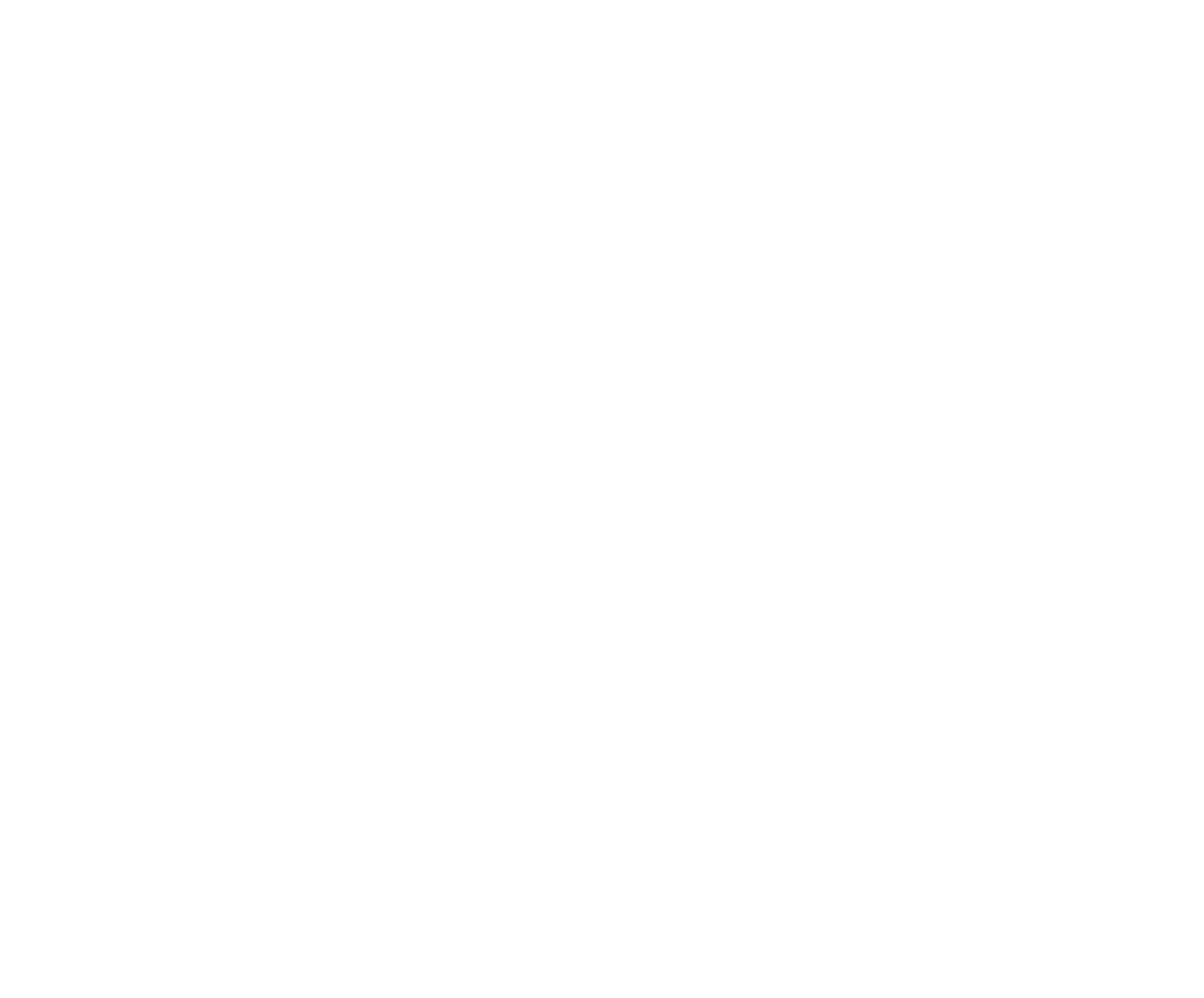
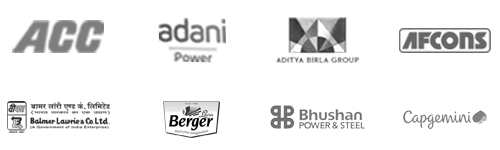

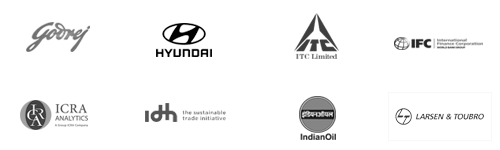
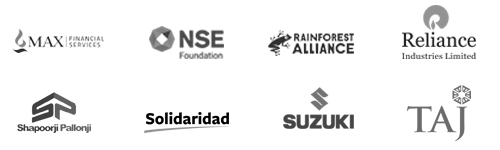
Resources at strategic locations
PAN India
Mumbai, Kochi, Thane, NCR, Indore, Bengaluru, Chennai, Kolkata, Visakhapatnam, Guwahati, Jamshedpur
Our Presence
100+ Thermographic Testing Projects
in last two years
India, SAARC Countries & Middle East
Ready to serve anywhere you are
14+ years
at the forefront of Safety Advisory Space
20+ types of Industry Sectors
Covering Manufacturing, Mining, Food Processing, Power & Utility, Warehouse, Construction, Services, FMCG, Logistics and Many More.
Thermographic Test or Thermography Test Services
Thermographic Test or Thermography Test Services for your Electrical Panels and Systems helps you to manage your electrical and fire safety risks. Thermographic test or electrical thermography or thermal imaging is the technique that uses an infrared imaging and measurement camera to “see” and “measure” invisible infrared energy being emitted from an object.
The objective of a thermographic survey is to identify abnormally high temperatures within electrical distribution systems.
- Experienced Resources - Electrical Engineers with qualification & expertise
- Detailed Report with Risk Priority and Recommendations
Thermography Test & Interpretation
Our Thermography Services ensure safety related to humans, the safety of equipment and workplace. The Delta T (temperature difference) criteria to evaluate the temperature severity of an exception. The Delta T recommended actions are mentioned below:
Featured solutions
Our Risk-Based Independent Third Party Fire Audit takes care of the fire-related issues and hazards in a plant, warehouse, facility or high rise building.
Commercial High Rise High Risk Buildings, Residential Complexes, Hospitals, Hotels, Shopping Malls, Educational Institutes, Warehouses
Solutions - How Consultivo can help
Remote Support
On-site Support
Blended support remote & onsite
Consultivo partners in your Safety Excellence journey
Our Risk-Based Independent Third Party Fire Audit takes care of the fire-related issues and hazards in a plant, warehouse, facility or high rise building.
Comprehensive, scientific & holistic approach to assess the potential of an outbreak of fire and provide solutions for mitigation.
Commercial High Rise High Risk Buildings, Residential Complexes, Hospitals, Hotels, Shopping Malls, Educational Institutes, Warehouses
We develop scenario based plan for a particular highly hazardous process area or equipment with reference to site emergency response plan.
It describes the fire protection and emergency response systems to be used in specific fire scenarios.
Emergency Response Plan | ERDMP (Emergency Response and Disaster Management Plan) | Emergency Preparedness and Response Plan
Fire and Electrical Safety Audits help organisations to identify & control both Fire and Electrical Safety Hazards together. They are actually interrelated in many aspects.
Acquire individual professional qualification or get your people trained on various methods of fire prevention and mitigation.
8.
- ERT Mock Drill
Emergency Response Team Training is an important tool for Emergency Preparedness Plan and Business Risk Management.
Emergencies can create a variety of hazards for people in the impacted area.
9.
Fire load, or more accurately fire load density is the starting point for estimating the potential size and severity of a fir
10.
- Mock Drill Review, Practice and Handholding
Master your Emergency Response Mock Drills!
Mock drills are one of the most important factors for emergency preparedness. It depends critically on human elements.
11.
- Fire Installation Review Programme (FIRM)
Many a time, the end users & facility owners do not have updated information about the adequacy of the installed fire protection system. Over the years, changes in infrastructure, occupancy, fire load and people affect the efficacy of the system.
Thermography Test For Electrical Panels – Approach & Methodology
Our Thermography Services are delivered in line with a robust methodology. It includes:
- Pre-Audit Meeting (opening meeting) with electrical maintenance team and related departments, identification of the target electrical equipment, installations and systems to define the scope of the audit such as Incoming supply receiving section, main sub-station, electrical equipment installed in various process sections, cabling, earthing system
- On-site electrical thermography applications on the selected spots and equipment to identify hazards as per the scope of the audit
- Discussion with Safety and Electrical personnel and sharing information of hotspot observed during thermography.
- Submission of draft Thermographic test report to the client containing Risk Based findings and observations with thermal imaging and recommendations
- Receiving inputs from the client on the draft report
- Submission of final electrical thermography test report
THERMOGRAPHY at a glance
A thermal imaging technique that is used to measure invisible infrared energy being emitted from an object
A loss prevention tool – supports comprehensive electrical & fire safety audit
PURPOSE
To identify and document exceptions (abnormally high temperatures) within electrical distribution systems and/or rotating equipment.
INDICATOR
Delta T (temperature difference) criteria is commonly used to rate the temperature severity of electrical and mechanical system exceptions.
POSSIBLE CAUSES OF EXCEPTIONS
Electrical systems
Deteriorated connections, short circuits, overloads, load imbalances, faulty or improperly installed components.
Rotating equipment
Friction due to improper lubrication, misalignment, wom components or mechanical loading anomalies
INSTRUMENT
Infrared thermal imaging systems with spectral range from 2 to 14 um and minimum resolvable temperature difference (MRTD) of 0.3°C or less at 20°C.
A spot radiometer or non- imaging line scanner is not sufficient.
THERMOGRAPHER
Preferably an electrical engineer with certified Thermographer’ qualification and competence
CODES AND STANDARDS
NFPA 70B, NFPA 70E, OSHA 29 CFR, NETA, ANSI, IEEE and NEMA
BENEFITS
- Helps to evaluate temperature severity objectively
- Identifies possibilities of electrical fire
- ensures safety to humans, equipment & workplace
Be a Consultivo Academy Certified Professional
QUALIFICATION, AWARENESS & COMPETENCE BUILDING
Online and Onsite Courses: Use our Training and Capacity Building expertise in Sustainability, CSR, Social Responsibility, and Social Governance.
- Featured training courses
Get to know all the elements in your report and how we can help you
You may also like
LEADING IN INDEPENDENT SAFETY SOLUTIONS – PAN INDIA
50+
Solutions
600+
Customers
30+
Industry Sectors
1500+
projects In total
22+
States
20+
Languages
Standards Used for Thermography Test for Electrical Panels
- NFPA – 70B
- National Electrical and Testing Association (NETA)
Find out more in NFPA
Thermography Operator | Competence & Qualifications
An electrical engineer and certified ITC (Infrared Training Center) ‘Thermographer’
Infrared Thermography for Industrial Applications
Infrared or IR Thermal imaging is an extremely useful tool for electrical safety through electrical panel thermography. It requires no contact being made with the components which means that the components can be checked in a live state, there is no effect on the components or interruption in any processes the electrical system may be controlling.
Instruments used for Thermography Services
Thermal Imaging Camera, Make FLIR, Model E60
Let's discuss
Browse our Case Study
Read a few of our stories as we partner organisations as an ESG, Sustainability and People Advisory Consulting Firm.
Featured Insights
Knowledge Bank
ESG Guide Book for Safety Experts – Focusing Safety Leadership
News & Events
Consultivo as the Technical Partner of CII Safety Symposium & Exposition 2023
View more in Impact Stories | Blogs | Knowledge Bank | News and Events
Curiosity Zone
Some more answers to your questions – FAQ
What are the possible electrical faults those can be prevented with Thermogrphy Tests?
Electrical faults can lead to breakdowns and the potential for fire hazards.
In both cases, the losses due to downtime and repair costs can become costly. Electrical equipment can suffer from numerous faults which will show an increase in temperature. Few of the causes could be:
- Corroded or loose connections
- Imbalanced Loads
- Using underrated equipment or overloading equipment
- Insulation Damage, Incorrect voltage
- Blocked or poorly ventilated equipment
- Deterioration due to age
- Exceeding the recommended temperature rating
Thermographic Tests support Electrical Safety Audits with data based evidences.
As one of the leading OHS Consultancy Agency in India and it’s neighboring countries, Consultivo provides independent and unbiased industry specific solutions in the areas of Hazardous Area Classification, Fire Safety Audit, Electrical Safety Audit, Electrical and Fire Safety Audit, Warehouse Safety, Safety Legal Compliance and many more.
View our complete range of Safety Consulting Solutions
How often should thermal imaging be carried out?
Frequency of Thermographic Test or Thermography Test for Electrical Panels – Thermal Imaging
The frequency of Thermographic tests for electrical panels varies depending on various conditions. A few of them are listed below:
- When environmental conditions are influential like wet and humid weather, corrosive condition
- Frequent failure due to temperature rise in certain nodes
For all practical purposes, Thermal imaging for all your electrical panels and related systems should be carried out every 12 months and more frequently if deemed so. In fact, many times, it has become a prerequisite for insurance renewals (which is yearly).
GLOBAL Experience